High efficiency sewing machine servo motor VS clutch motor -- Sewing Machine Motors Productivity is the Key
Only by energy savings through Servo Motor additional cost of machine can be recovered in approximately 4 years. However, other advantages like time savings and thread cost savings will make the actual return on investment faster. Last, but not the least this initiative will also entitle your organization for ‘green’ points.
The performance of a sewing machine is largely affected by the control it gives to operators. If the machine can be controlled easily, so is the quality of the garments produced by machine. The operator can speed up the machine and slow it down according to the requirements of the precision of the seam being sewn. Clutch Motors and Servo Motors are two prime options available to the Sewn Products industry to meet their needs of powering the sewing machine. Team StitchWorld along with Y.P. Garg, a sewing machinery expert, Anshuman Dash from Loiva and Suneet Kamra from Divshum International analyzes the advantages and disadvantages of Clutch and Servo Motors.
Clutch Motors
Clutch motor system is made up of three parts: Tri-phase induction motor (which is a normal AC current motor), a clutch and a belt pulley. The induction motor uses three-phase alternating current supply and it usually works with efficiency lower than 75%.
Traditionally Clutch Motors have been running the sewing machines in most of the factories at least in India. These motors run on Alternating Current (AC) and gain speed up to 2850 RPM within a span of a few seconds like the electrical fans. Once they attain the full speed, they keep running at it, irrespective of whether the pedal of the machine is pressed or not.
This means that irrespective of the fact that the needle is not moving, the motor rotates at the rated speed and consumes electricity at its rated wattage (usually 400W). This particular feature makes Clutch Motors better suited for longer seams where the operator has to sew half-a-metre at a stretch like bed-sheets, table linens, etc. This is because for longer seams, the time for which the electrical energy is used for moving the needle is more. In particular, for overlocks where not much skill is required for operation, Clutch Motors are preferred.
Also, for projects that include heavy material such as for saddles, harnesses, leashes and other thick materials, Clutch Motors are recommended. For sewing at a normal speed with Clutch Motors it can be pointed out that clutch output (i.e. speed of rotation of shaft) is changeable but its input, i.e. the rotation speed of the motor, is constant. This leads to high power losses, in particular at lower output speeds.
Disadvantages of Clutch Motors
The biggest problem with Clutch Motors is that any uncontrolled pressing of pedal of the sewing machine makes it run at full speed. The desired speed can only be achieved by an experienced operator. Clutch Motors are not much profitable for short and curved seams.
It should also be ensured that the operator doesn’t waste thread when using sewing machine with Clutch Motors. If the operator is unskilled and wastes thread and time for trimming, then Servo Motors should be preferred as UBTs (Under Bed Trimmers) are compatible only with them.
Clutch Motors often get heated or overloaded when the motor is switched on. This is often termed as starting overload. As the torque in a Clutch Motor is proportional to the RPM, on starting the motor, any resistance to motion of the coil can easily stop it and cause heating and overload.
Overloads can happen even when the machine is in running condition. The reasons could be wornout parts or lack of lubrication. Even the material (leather, textile etc.) being worked upon can contribute to an overload. Both Servo and Clutch Motors are prone to running overloads but the possibility is far less in a servo due to high torque that it generates.
Servo Motors
The Servo Motor system contains two parts, namely Servo Motor and belt pulley. The Servo Motor with strong magnetic forces can reach a high speed and high efficiency usually above 80% and maximum up to 95%.The maximum speed at which it can run is over 4000 RPM. With the use of electronic controller it is easier to control the start and stop speed and output forces depending on specific sewing requirements.
Advantages of Servo Motors
Servo Motors are computerized DC motors, which is the reason why they are getting popular in the industry. Like the most DC motors, they go in stand-by mode when shaft is not moving and consume just 0.1A to 1.8A, i.e. a power consumption of about 1W. Sewing machine, in fact consumes electricity not only for the time the pedal is pressed but also in proportion with the speed at which it is running, i.e. a 550W Servo Motor will consume 550W when the machine is running at the maximum speed (around 4000 RPM). If the machine is run at half the speed, let’s say 2000 RPM, then the motor will consume electricity at half the rate, i.e. 275W.
This is great savings! Around 80-92% of the time is spent on handling the garment and all this time,the machine needle is at rest. Had it been the traditional Clutch Motor, the electricity bill would have been for the entire day despite the fact that the needle moved for less than 20% of time.
Besides, running the machine at the desired speed, Servo Motors allow fitting of needle synchronizer, which controls the needle position every time the machine stops. One can be sure that whenever the machine stops, the needle will be positioned inside the fabric or at its highest position, allowing the backtacking to be done automatically and smoothly, unlike Clutch Motors where the operator has to press the backtack lever using his right hand. Many a times, in machines with Clutch Motors, when only 1 to 2 stitches are required on a garment part, the operator has to rotate the machine head manually. This means that because of the uncontrollable speed of the machine, the operators are using their hands to do it, which means further loss of energy as well as time.
The Servo Motors come with an option of variable speed adjustment, from 400 RPM to 4000 RPM. This is impossible to attain on sewing machines having Clutch Motors.
Most people in the world, including the operators are right handed. They prefer using their right hands for high-precision or skilled work. Yet, when it comes to sewing, the right hand of the operator does much less important functions in a Clutch Motor powered machine –
Pressing the backtack lever before starting the stitch.
Controlling the machine head while starting and ending the stitch line so that sewing is slow enough to perform backtack operation.
Re-pressing the backtack lever at the end of the switch followed by rotating the machine head by hand to bring the needle up.
Cutting the thread using a scissor or a thread trimmer.
Only in the remaining time (in a sewing cycle), the right hand handles the fabric, which is quite surprising considering the quality demands of perfect seams with perfect stitches, but all this has to be done mostly using left hand of the operator.
A Servo Motor powered machine makes the situation easier by ensuring, through a synchronizer, that the needle is out every time the machine stops; presser foot lifter will lift the presser foot every time the machine stops. Thread will be cut automatically using UBTs. Backtacking will be done automatically. Start and end speed of a sewing cycle can be made slower by motor adjustments, so that no matter how much force you exert on the pedal, the machine is just at perfect speed for you to focus and pay attention to perfect handling of fabric with both hands. And above all, the operator will have both his hands free to handle the fabric and concentrate on the quality of seams produced. So, Servo Motors not only saves power but also help save operation time.
Just imagine if all these functions of the Servo Motors save you 5% of the time, your productivity may increase substantially, about 25%. Add to this the improved quality due to better handling. The counter-argument to this can be that the Servo Motor powered machines are pretty expensive. This is because to make all those functions work (automatic backtack, needle positioner/synchronizer, etc.) you need some extra devices which add to the price of the machine. But, the motor’s cost can alone be recovered in less than a month. The rest of the tools only add to your productivity, thereby speeding up the recovery process.
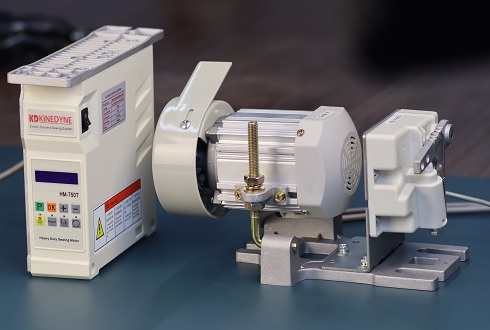
Click here for original work
Click here for 3D Dynamic Video
Click here for specification |